Figure 4® シリーズ / 医療
補聴器メーカーがFigure 4ソリューションで、硬質・ゴム製の製造用樹脂を3Dプリントすることにより製造課題を解決
補聴器業界を牽引する世界的メーカーのWS Audiology社は、3D Systems社の高速3Dプリンター“Figure 4”を採用。同社が構えるデンマークのリンゲ拠点にて、量産グレードのグリッパ、固定具、試作品の3Dプリントを行い、射出成形製造プロセスの品質と機能を向上させました。
補聴器シェルの製造に3Dプリントを採用した先駆者であるWS Audiology社は、製造ラインや製品開発の様々な課題を解決するために3Dプリントの利用範囲を拡大しており、Figure 4の品質、性能、材料の汎用性の高さが主なメリットであると言及しています。
医療
WS Audiology社
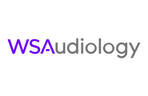
「造形品質、生産能力、材料の幅広さの点から、Figure 4が当社のニーズに最適な
ソリューションであることが早い段階から分かっていました」
- WS Audiology社 ツールデザイナー Henry Frederiksen氏
課題
小型部品搬送の質と機能の向上
WS Audiology社のWidexブランドの補聴器には、様々な種類の射出成形部品が数多く存在します。
そのような部品には、補聴器内に収められる電子部品のケーシング、接点、ブロックなどがあり、なかには8mm×3mmの小さなものもあります。
このカテゴリの部品はサイズが小さいため、人の手ではなくロボットで取り扱う必要があり、比較的大きな部品には吸着カップを、小さな部品には金属製のグリッパを使用します。
しかし、これらの取り扱い方法には欠点があります。吸着カップでは部品の向きを適切に調整することが難しいためグリップ力が低くなり、金属製のグリッパは部品に傷をつけやすく、製造リードタイムも長くなります。
ソリューション
1. 高精度3Dプリンティング
WS Audiology社は、補聴器シェルの製造に3Dプリントを使用することで、最終製品の品質を大幅に向上させ、生産性が8倍向上するなど、いくつかの大きなメリットを得ることができました。
この成功を受け、同社がワークフローで抱えていた搬送の問題を解決するために3Dプリントの適用範囲を拡張することが決定されました。
Figure 4は、非接触膜技術を使用して、精度と驚異的なディテールの忠実性を超高速のプリント速度で実現させる投影型の積層造形テクノロジです。
WS Audiology社では、Figure 4® Standalone使用しています。
スピード、品質、精度に加えて、産業用グレードの耐久性、サービス、サポートを提供し、容易な材料交換によってアプリケーションの多用途性を高めています。
2. 迅速な設計の反復
このタスクは、WS Audiology社の金型部門が担当することになりました。
金型デザイナーのHenry Federiksen氏は、Figure 4を使用することでプロジェクト成功の自信を深めることができ、ソリューションのスピードアップによって短時間でより多くの部品を製造、テスト、確認することができるようになったと述べています。
3. 生産速度
Figure 4 を使用する主なメリットに、金型を使わずに部品を製造できることがあります。
WS Audiology社は、デジタルファイルから部品を直接製造できるメリットを活かし、一般的な製造プロセスから大幅に時間を短縮することができました。
Frederiksen氏によると、3Dプリントによるグリッパは1日~2日で入手できるため、射出成形部門の多くの顧客を満足させることができているとのことです。
「現在の生産量は、年間でグリッパが約200個、治具と固定具が約100個、プロトタイプが500個以上となっており、投資を有効活用できています」
- WS Audiology社 ツールデザイナー Henry Frederiksen氏
4. 製造能力の高い材料
WS Audiology社の金型製造アプリケーションは、Figure 4 PRO-BLK 10とFigure 4 RUBBER-65A BLKを活用しています。
Figure 4で使用可能な材料の幅広さは、材料特性の多様性を高め、屋外部品では最長1.5年、屋内部品では最長8年(ASTM試験法による)の長期使用を想定して設計された材料の化学的性質により、幅広い用途への使用が可能です。
Figure 4 PRO-BLK 10は量産グレードの硬質材料であり、Figure 4 RUBBER-65Aはショア65A硬度と優れた破断点伸びを持つ、程よい引裂強度を備えた量産グレードのゴムです。
結果
より良い性能の部品を迅速に提供することで、性能、多用途性、納期を改善
- 部品をより早く入手
1~2日で納品 - ソフトグリップの導入
傷がつきやすい金属グリップを置き換え
- 生産量の増加
年間数百個のユニークな部品をプリント - アプリケーションの多様性
グリッパ、治具、固定具、プロトタイプなどに適用