ProJet® MJP 2500Plus / 消費材
“人だけを涼しく”
革新的な熱中症対策品の開発には3Dプリンターが欠かせない存在に。
株式会社セフト研究所様(以下、セフト研究所:https://www.seft.co.jp/)は、空調服®をはじめ、寝具やリュックに至るまで夏場の様々な熱中症対策品を製造、販売するメーカーです。
空調服®を構成する電気部品の開発、設計を行う技術部 井上氏に3Dプリンターの活用について伺いました。
株式会社セフト研究所 様
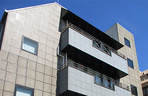
ファン付きウェアを発明したパイオニア
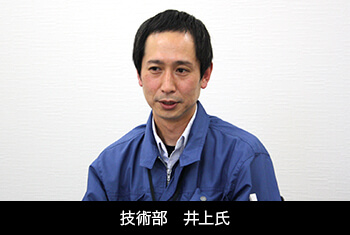
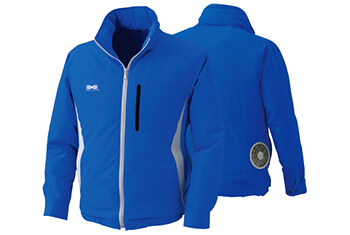
イグアス:セフト研究所の空調服®についてお聞かせください。
井上氏:セフト研究所が製造している空調服®は『生理クーラー®(暑さを脳で感知し、それにより出た汗を蒸発させて体温を下げる)』の原理を利用し、身体と衣服の間に効率的な空気を流すことで、適切な冷却を可能とする製品です。人が身に付ける製品の為、安全性には特に注意し、不良率を限りなくゼロに近づける努力を日々取り組んでいます。他のメーカー様も含め、多くのファン付きウェアが販売されている中、弊社では「より効率的、より快適、より安全な」をモットーに軽さや風量にこだわりながら、最適な冷却性能をお客様に届けられるよう、細部に至るまで追求しています。
イグアス:現場で働く方向けの作業着になるのでしょうか?
井上氏:お客様は外で働く建設業界の方や工場の方々が中心にはなりますが、アパレルメーカー様やスポーツ用品メーカー様ともコラボレーションを行い、普段着としても着用できるようフィンガーガードのデザインも機械形状から有機形状のデザインに変更し“かっこよさ”も取り入れています。
お客様の声を反映したより良い製品づくり
イグアス:製品づくりの中でどのように3Dプリンターを活用されていますか?
井上氏:空調服®のメインパーツとなるファンやバッテリーの試作品製作に3Dプリンターを活用しています。毎年、翌々年の夏に向けた新商品開発を行うのですが、前回を上回るより快適な風量を実現するためには様々なモデル作成や検証を行わなければならなく3Dプリンターが活躍します。
特にファンは、プロペラの角度や枚数、フィンガーガードの形状により風量や効率が大きく変わります。お客様から『極力軽くして欲しい』とご要望をいただくのですが、ファンを軽くしすぎると強度に問題がでてしまう為、強度と風量の絶妙なバランスの設計を心掛けていますね。
ファンの設計シミュレーションでは、最低でもモデルを3~4パターン選定して3Dプリンターで造形します。造形したものに対して実際にモーターを取り付け、実製品と同じように風量や効率測定を行う手順を繰り返します。
バッテリーについては、ケースを3Dプリンターで作成し、デザインやサイズ感、基板やリチウムイオンセルをケースに組み込むときの作業性等を確認しています。
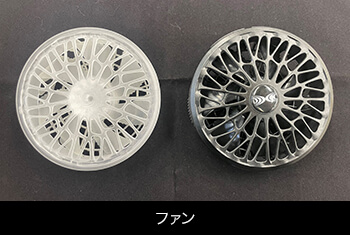
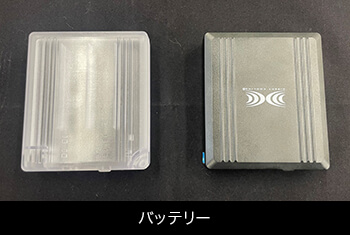
繰り返し検証が製品開発の“カギ”
イグアス:3Dプリンター導入前後の変化について教えてください。
井上氏:当社製品開発の特徴として、少しの形状変更で風量効果が変わる為、試作品での検証は非常に重要になります。
3Dプリンター導入前は、外注で試作依頼をしておりましたが、国内ではちょっとした試作品を作るにも費用が高く、コスト面から容易に様々なモデル検証を行うことができない状況でした。
また、弊社中国工場で保有するインクジェット式3Dプリンターで造形を行うこともありましたが、輸送に時間がかかり、設計してから試作品を確認するまでに多くの時間を要していました。
毎年限られた製品開発の時間の中で多くの検証を行うためには、自社でも試作品が内製できる必要があり、高性能な3Dプリンターを2年前に導入しました。
3Dプリンターを導入したことにより、ほとんどが設計した翌日には試作品を確認できるようになり、開発スピードが大幅に上がりました。
開発スピードが上がったことで、課題抽出→再設計→試作→課題抽出・・・を繰り返せるため、よりよい製品開発に繋がっていると実感していて、今では“なくてはならない”ものになりました。
ProJet 2500Plus導入の決め手は“後処理”
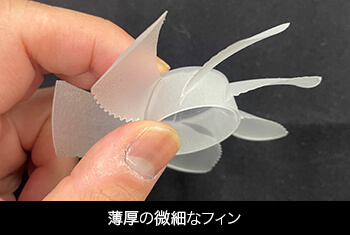
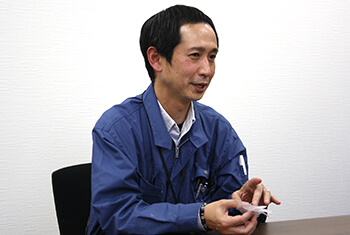
イグアス:3Dプリンターを導入する上での選定ポイントを教えてください。
井上氏:実はProJet 2500Plusを導入する前に他社のインクジェット3Dプリンターをレンタルで使用していました。出来栄えがきれいで良かったのですが、水圧洗浄でのサポート材除去を行う必要があった為、薄くて細かいフィンが欠けてしまうことが度々あり、美観が損なわれ苦労しました。
そこで購入する際の機種選定は、「造形物を破損させることなく精細な造形が行えること」を優先しました。結果、ProJet 2500Plusが最も要件を満たしていたので、導入を決めました。
ProJet 2500Plusの後処理工程は、恒温槽内でサポート材を熱で溶かす方法のため、水圧等による破損のリスクがなく、美観を傷つけずに処理が行えます。
また、表面が滑らかで寸法精度も良いため、加工をせずにフィンガーガードとの嵌合確認が行え、実製品と比較しても近似値の風量測定結果が出ています。
使用してみて気づいた点ですが、造形ごとにヘッド清掃が不要でメンテナンス頻度が低いため、今まで3Dプリンターを使用したことが無かったメンバーでも簡単に使用できる点も良かったです。
● 破損のリスクが無い、置いておくだけの簡単なサポート除去
● 金型成形品と比較しても遜色ない出来栄え
● 3Dプリンターが初めてでも気軽に使える操作性・メンテナンス性
今後の3Dプリンターに望むこと
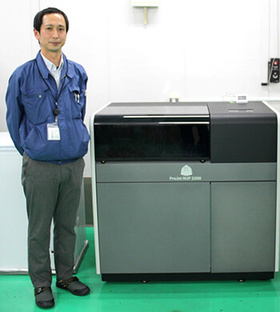
イグアス:これからの3Dプリンター活用についてお聞かせください。
井上氏:空調服®の技術は、服だけでなくその他にも様々な分野で適用できると考えております。新製品開発にあたって今まで成形利用していたABSだけでなく、ゴムやシリコンといった弾力性のある材料も検討しているため、3Dプリンターで試作利用できればと考えています。
最近では最終部品造形用途の3Dプリンターも出てきているので、特注品の小ロット生産や改良品のリペアーパーツなどに利用できたら面白いかもしれません。これからも3Dプリンターを利用して製品開発を行い、暑さに悩むひとを快適に、笑顔にしていきたいです。
「空調服」は(株)セフト研究所・(株)空調服のファン付きウェア、その附属品、及びこれらを示すブランドです。
「空調服」「
